01
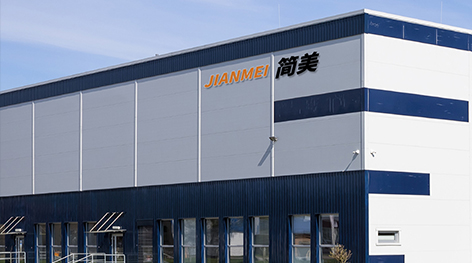
Welcome to visit
our factory workshop
The Xuzhou Jianmei Glass Products Factory workshop covers an area of about 50,000 square meters, of which 15,000 square meters are storage area and 2,000 square meters are packaging area.
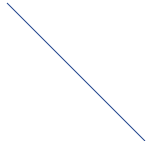
JIANMEIGLASS furnace equipment is used to make raw materials for high borosilicate glassware. We cover an area of about 2,000 square meters. The overall area is distributed as follows: blowing equipment, pressing equipment, tube drawing equipment, annealing furnace, cutting equipment, edge grinding equipment, as well as testing equipment and crane and forklift equipment.
02
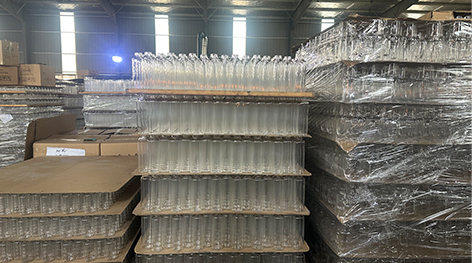
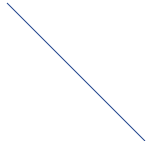
03
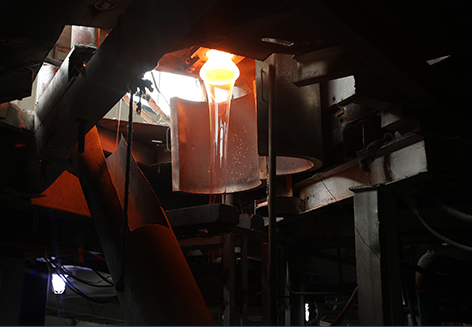
Melting equipment
Select high-purity quartz sand, borax, boric acid, and aluminum oxide as raw materials. Weigh and proportion them according to precise formula ratios, and then fully stir them evenly in a mixing device.
Add the prepared raw materials into the furnace. First, heat up to 800 – 900°C to prompt the solid-phase reaction of the batch materials and form silicate sintered products. Then, raise the temperature to 1200 – 1500°C. At this time, the silicate sintered products gradually melt and the glass begins to form. Finally, heat up to 1400 – 1750°C to enter the glass liquid clarification stage, allowing bubbles to escape. During this period, an appropriate amount of fining agent can be added to assist and ensure the purity and transparency of the glass liquid.
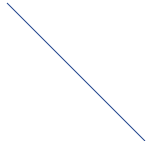
Forming Operation
When the glass liquid reaches the appropriate forming temperature, use forming processes such as blowing, pressing, or drawing to shape the glass liquid into the initial bottle blank. When blowing, precisely control the air pressure of the blowpipe and the blowing time to ensure uniform wall thickness of the bottle blank. When pressing, adjust the mold pressure and temperature to ensure forming accuracy.
04
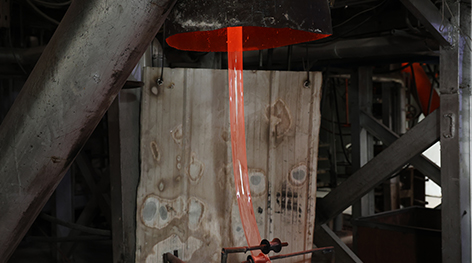
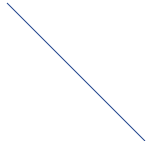
05
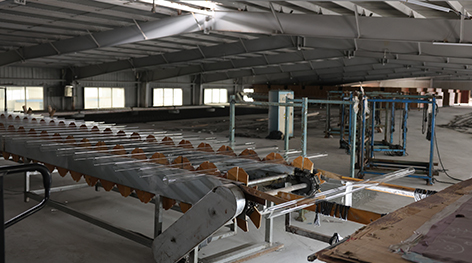
Cutting equipment
According to product design requirements, select a glass cutter or a grinding wheel cutting machine to cut the bottle blank. When using a glass cutter, make a scratch on the surface of the bottle blank with a depth of about 1/3 – 1/2 of the wall thickness, and then carefully break it off. When using a grinding wheel cutting machine, fix the bottle blank and adjust the cutting speed (for example, for pipes with a diameter of 10 – 20mm and a wall thickness of 2 – 3mm, the cutting speed is controlled at 5 – 10mm per minute) for cutting.
After cutting, use sandpaper from coarse to fine (for example, first 100 – 200 mesh, then 400 – 600 mesh) to grind the cutting edge in turn to make it smooth and flat without burrs.
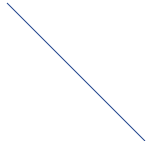
Back cover machine
Select bottle bottom blanks that meet the dimensional accuracy requirements and are of qualified quality, and heat the edges to a softened state, usually using a flame spray gun. The temperature is controlled near the glass softening point. Precisely butt the softened bottle bottom blank with the bottom of the bottle body and apply appropriate pressure to make them fuse at high temperature. After that, put the bottom-sealed bottles into the annealing furnace and use an appropriate annealing curve to eliminate stress and prevent the bottles from cracking.
06
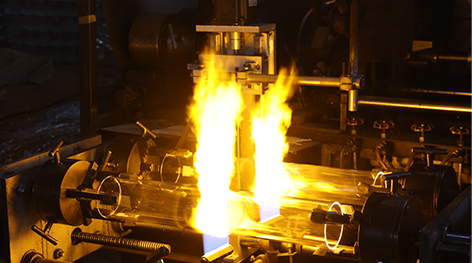
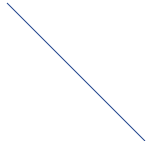
07
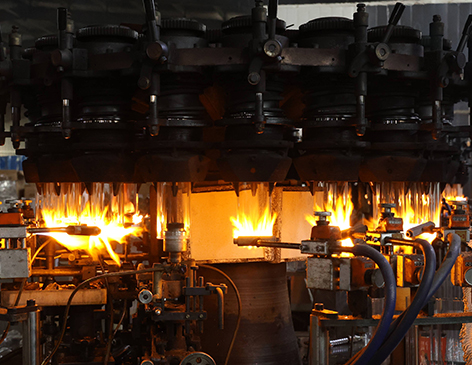
Sealing machine
For the initial forming of the bottle mouth, reserve an appropriate size by controlling process parameters during the bottle blank forming stage. If precise treatment is required later:
Cutting: Use a diamond grinding wheel to accurately cut the bottle mouth, control the cutting depth and angle to ensure a flat cut, and the flatness error is controlled within ±0.1mm.
Grinding: Use sandpaper or grinding wheels of different particle sizes to grind from coarse to fine to remove burrs and cutting marks and maintain the roundness of the bottle mouth.
Flame Processing: When a special-shaped bottle mouth (such as a constricted or flared mouth) is required, heat the bottle mouth to 800 – 1000°C with a high-temperature flame spray gun, and use a mold or tool to squeeze (constrict) or expand (flare) while rotating the bottle to ensure uniformity.
Cold Working: When necessary, use CNC machining equipment to precision mill the bottle mouth and control the dimensional tolerance within a very small range to meet the requirements of high-end products.
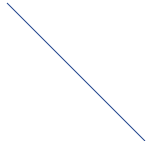
Decal Raw Materials
In a dust-free workshop, first use a special glass cleaner and a soft cloth to thoroughly clean the bottle body to remove impurities such as dust and oil stains.
Select suitable decal papers according to the bottle design, such as ceramic decal papers or glass-specific decal papers, to ensure firm colors and high-quality pattern printing.
If it is a water transfer decal paper, soak the cut decal paper for 20 – 30 seconds, and then gently transfer it to the bottle body with tweezers or a soft brush. If it is a self-adhesive decal paper, uncover one end of the backing paper, align it with the starting position and slowly uncover it. At the same time, use a soft cloth or a squeegee to squeeze from the center to the edge to expel air.
08
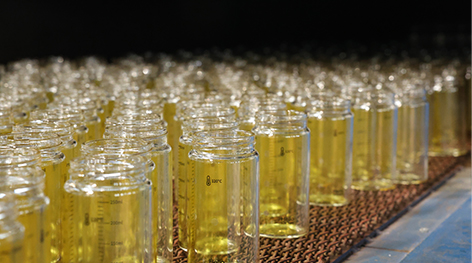
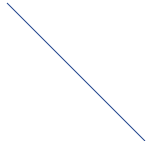
09
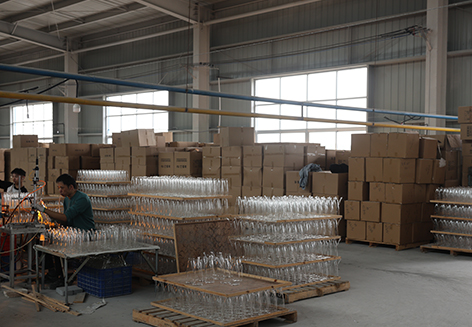
24m annealing
furnace equipment
After checking the firmness of the decal adhesion and ensuring there are no problems such as bubbles, wrinkles, or edge warping, place the bottles on a high-temperature-resistant bracket or tray, keep a certain distance, and put them into the firing furnace.
Control the furnace temperature at 550 – 700°C and heat up at a rate of 5 – 10°C per minute. Depending on factors such as the size of the bottle and the thickness of the decal, the firing time is controlled at 40 – 90 minutes to make the decal pigment melt and solidify. During this period, keep the temperature and atmosphere in the furnace stable.
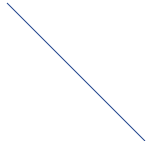
Finished Product
Inspection
Conduct a comprehensive inspection of the fired finished products, including appearance (decal integrity, presence or absence of bubbles, wrinkles, discoloration, etc.), dimensional accuracy (whether the sizes of the bottle mouth, bottle body, and bottle bottom meet the standards), and performance (such as whether the corrosion resistance and heat resistance meet the standards).
If any defects are found, repair them in time or remove unqualified products.
10
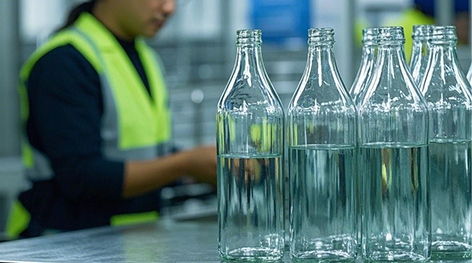
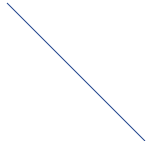
11
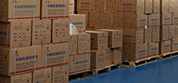
Packing and Shipping
According to factors such as the specifications and uses of the bottles, reasonably select packing methods such as individual paper boxes, bubble bags, pearl cotton, and card packaging. For example, for fragile and high-precision bottles, pearl cotton is preferably used to wrap them before packing. For bottles for ordinary use and in large quantities, simple protection with bubble bags before packing can be used.
Place the packed products neatly, mark them clearly, and deliver them for transportation.
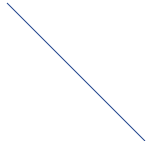
The above is about the current production workshop configuration of our factory. We are proud to have 45 appearance patents and 32 intellectual property rights, as well as 120 testing certifications. Including FDA, CE, ISO9001, ROHS, LFGB, BSCI, etc.
12
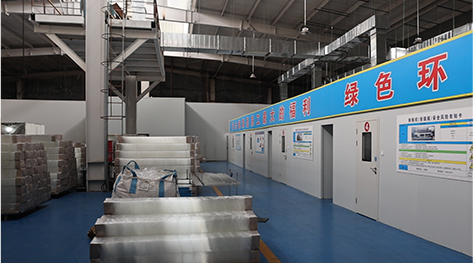