Customizatione
Packaging Customization
Packaging Solutions
High borosilicate glass is widely used in precision products such as laboratory utensils and heat-resistant cookware due to its excellent high temperature resistance and low thermal expansion coefficient. Its molding process is diverse, some processes require molds, while others do not. Glass bottle molds are key process devices for molding glass products, which are used to fix the appearance of glass bottles. There are many types of glass bottle molds. Their design and manufacturing are usually carried out after the design of the glass bottle is completed, and they are the core link of the technical work of the bottle factory. High-quality molds are the key factor to ensure that the glass bottle factory produces qualified products.
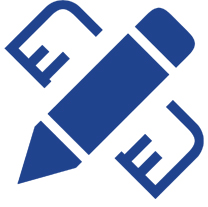
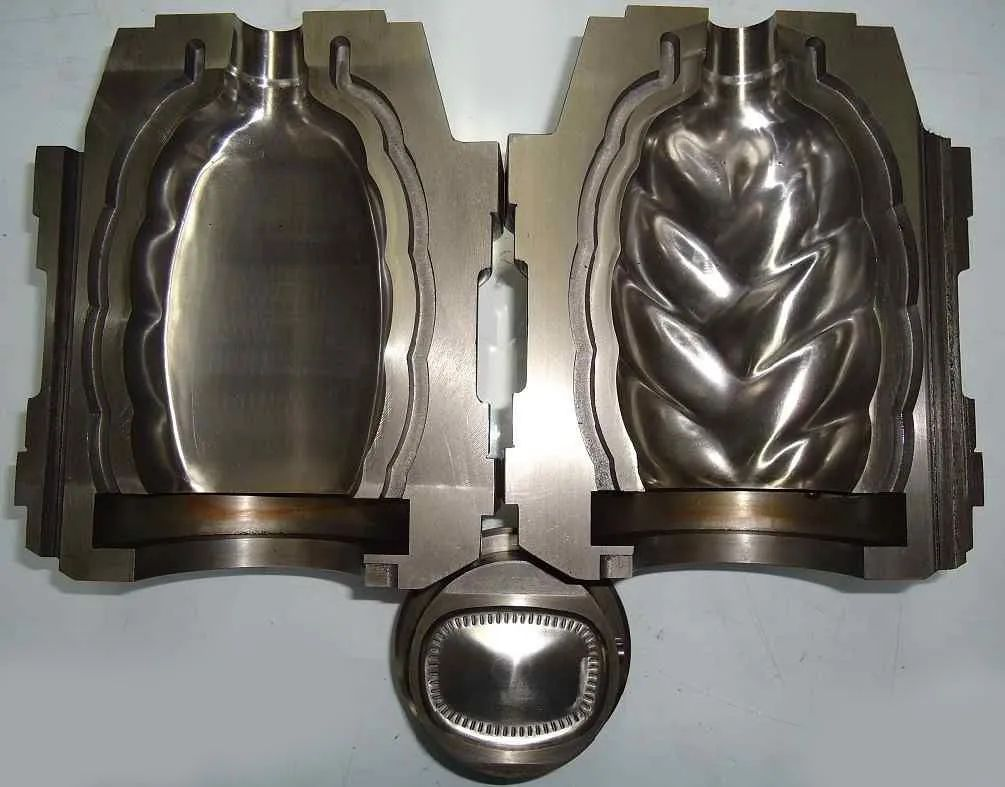
1 Molds according to structural types:
(1) Integral mold
(2) Removable mold
The removable mold is a combination of two symmetrical halves of the mold, which can be opened and closed. In order to avoid the mold from being misaligned when opening and closing, a concave and convex structure is made at the joint of the two molds to facilitate positioning.
2 Bottle making process is usually divided into two types:
blow-blow method for producing small-mouth bottles and pressure-blow method for producing large-mouth bottles.
The mold used for producing small-mouth bottles by blow-blow method mainly includes: mouth mold, core, mold, bottom mold, initial mold (also known as “initial mold”), funnel and blind head, etc. The mold used for producing large-mouth bottles by pressure-blow method mainly includes: mouth mold, mold, bottom mold, punch, initial mold, blind head, punch, cooler, etc.
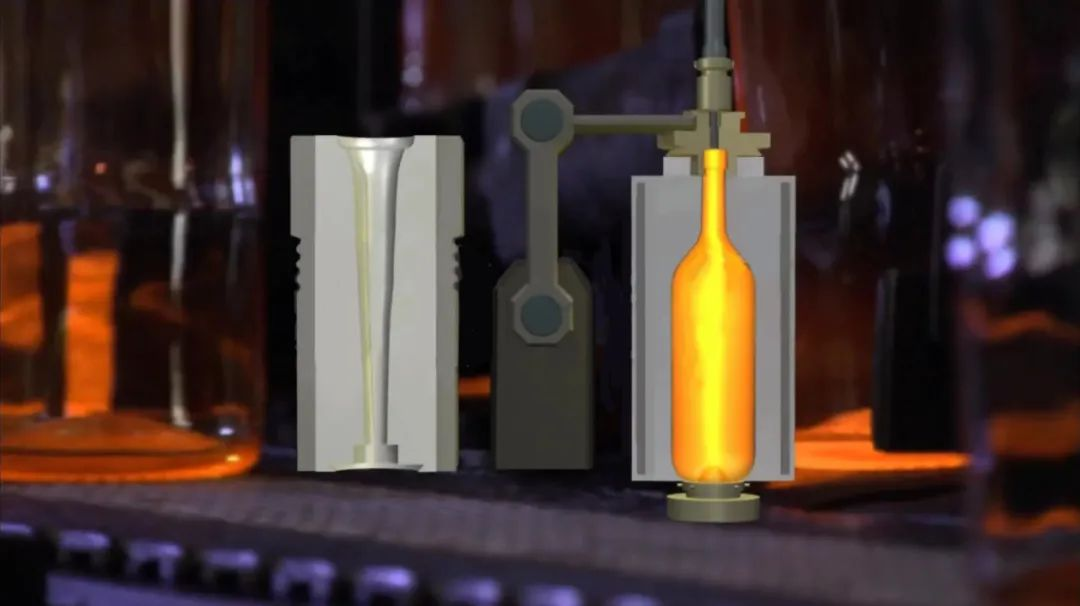
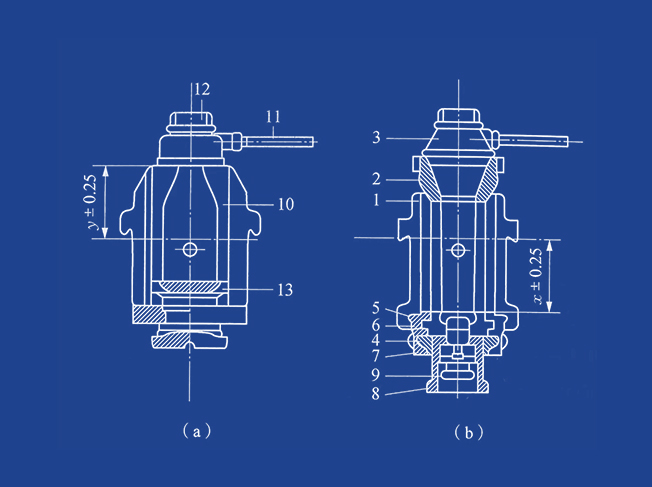
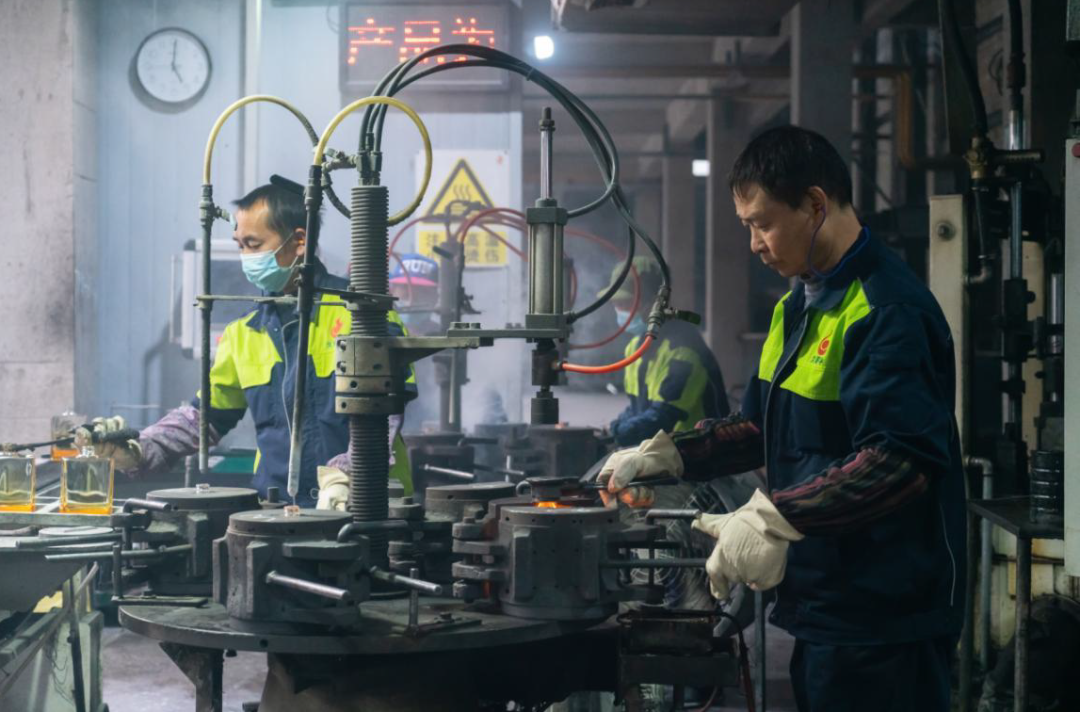
As far as mold design is concerned, the requirements for designers are to have rich mathematical knowledge (including advanced mathematics), be proficient in the structure of bottle making machines, bottle making processes and mechanical processing processes, and be proficient in the use of drawing software, etc.
After the design of the glass bottle is completed and determined, the design of the mouth mold, the mold and the bottom mold is relatively simple, while the design of the core and the inner shape of the initial mold in the blow-blow method, and the design of the punch and the inner shape of the initial mold in the press-blow method are more complicated and difficult. In particular, the design of the punch and the inner shape of the initial mold in the press-blow method has higher requirements for the designer.
Processes requiring molds
Pressing (compression molding)
Use: to make regular-shaped vessels such as cups, bowls, and plates. Process: The molten borosilicate glass liquid is injected into a metal mold, pressed into shape by mechanical pressure, and demolded after cooling. Features: The molds are mostly made of high-temperature resistant alloys (such as graphite or steel molds), suitable for mass production of standardized products.
Blowing molding
(mold-assisted)
Use: to make laboratory glassware such as beakers and flasks or vessels with complex shapes.
Process: Manually or machine-blow the glass liquid to the inner wall of the metal mold, use the mold to shape the outer contour, and then fine-tune it.
Features: Mold-assisted can accurately control the shape, but some processes still rely on manual operation.
Processes without molds
Drawing molding
Use: to produce long strip products such as glass tubes and glass rods.
Process: Directly stretch the desired shape from the molten glass liquid, and shape it by controlling the speed and temperature, without the need for a mold.
Float process
Use: to produce long strip products such as glass tubes and glass rods.
Process: Directly stretch the desired shape from the molten glass liquid, and shape it by controlling the speed and temperature, without the need for a mold.
Free-formed by hand
Application: Art glass products or customized products.
Process: The craftsman directly shapes with tools (such as blowing, stretching, bending), relying on experience and technology, without the need for fixed molds.
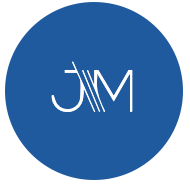
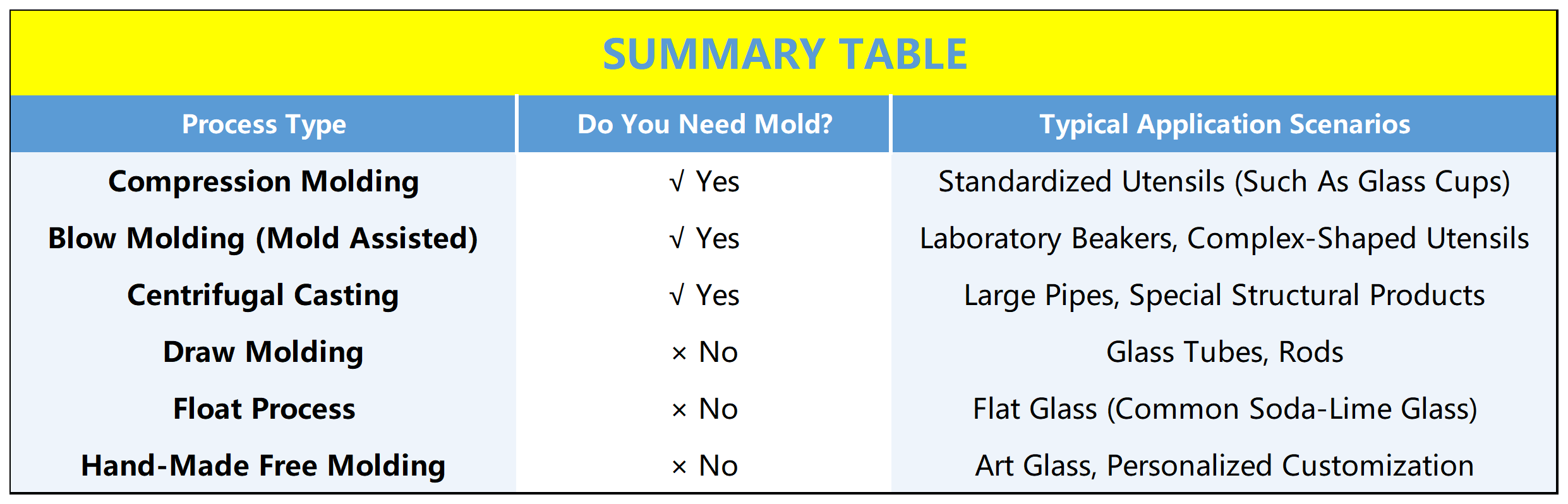
In the manufacturing process of high borosilicate glass, whether to use molds depends on the specific molding process. Molds play a key role in press molding and blow molding. They are used to make vessels with regular shapes or products with complex contours, which are suitable for mass production and precise control. For drawing molding, float process and manual free molding, molds are not required, which are more suitable for the production of long strips, flat glass or artistic customized products. High-quality mold design and manufacturing are the core to ensure the qualification of glass products, while the process without molds is more dependent on the operator’s experience and technology. In short, whether the mold is used or not depends on product demand and process selection. Both have their own advantages and jointly promote the diversified application of high borosilicate glass.